In an industry as highly regulated as chemical manufacturing, staying compliant with workforce regulations isn’t optional—it’s essential. From safety protocols to labor laws, chemical manufacturers must navigate a complex web of requirements to avoid costly penalties and protect their workforce. As regulatory scrutiny increases and labor laws evolve, the need for streamlined compliance processes has never been more urgent.
So how can chemical manufacturers stay ahead of the curve? The answer lies in proactive planning, workforce visibility, and modern technology built to support compliance at scale.
Understanding the Regulatory Landscape in the Chemical Industry
Navigating this complex regulatory landscape requires more than just awareness—it demands operational alignment. Chemical manufacturers must ensure that labor scheduling, skills tracking, and compliance documentation are not only accurate but integrated into daily processes.
This means building a workforce strategy that prioritizes safety, training, and real-time visibility into labor practices. With regulatory audits becoming more frequent and detailed, organizations can no longer afford siloed or manual approaches to workforce compliance.
Key Workforce Compliance Challenges for Chemical Manufacturers
Chemical manufacturers operate under some of the strictest environmental and occupational health and safety regulations in the world. Organizations must comply with OSHA standards, EPA requirements, and industry-specific mandates that govern the handling of hazardous materials and exposure limits.
Beyond environmental and safety compliance, chemical manufacturers also face unique workforce-related challenges. Labor agreements, union rules, and shift scheduling complexities can make workforce planning difficult—especially when dealing with 24/7 operations. Improperly trained or uncertified workers performing high-risk tasks can result in severe consequences, including regulatory citations or even facility shutdowns.
For more on this, see aligning labor rules and regulation.
The Impact of Evolving Labor Laws
The regulatory environment isn’t static. Recent updates to overtime eligibility rules, paid leave mandates, and fair scheduling laws have added new layers of complexity to workforce compliance.
Failing to stay up to date can be costly. Non-compliance may result in steep fines, reputational damage, or litigation. For example, if an employee is assigned to a task they are not certified for, or if records show excessive overtime without proper compensation, regulators can—and will—take action.
Chemical manufacturers must ensure that their scheduling practices, employee documentation, and compliance protocols are dynamic enough to keep up with these changes.
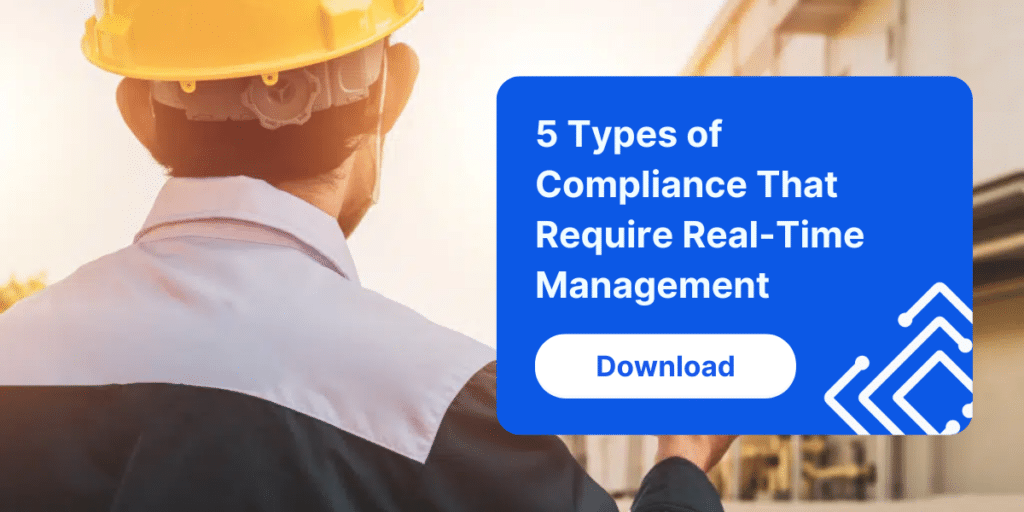
How Technology Can Simplify Compliance
As regulations tighten and operational demands grow, technology has become a critical enabler of workforce compliance. Modern solutions don’t just digitize outdated processes—they empower chemical manufacturers with the tools to proactively manage risk, ensure training alignment, and maintain compliance at scale. From scheduling to skills tracking, integrated workforce management platforms provide a single source of truth, reducing administrative burden while improving accountability across departments.
Automating Labor Scheduling and Recordkeeping
Manual processes are no longer sufficient to meet compliance demands. Automating workforce scheduling not only improves operational efficiency but also ensures every shift is filled by qualified employees. A digital scheduling platform can enforce pre-configured rules that align with regulatory requirements, preventing non-compliant assignments before they happen.
Equally important is recordkeeping. Chemical manufacturers need audit-ready documentation that verifies proper staffing, training completion, and time tracking. Automating this data collection ensures accuracy and accessibility when you need it most—whether it’s for internal audits or a surprise regulatory inspection.
Adapting to Regulatory Changes in Real Time
One of the biggest advantages of a cloud-based workforce management system is its ability to adjust on the fly. If a regulation changes—say, new restrictions on overtime hours for certain job classifications—you need a system that can enforce that change automatically.
Dynamic rule configuration allows chemical manufacturers to build compliance into the scheduling engine itself. This agility is especially valuable when responding to unexpected disruptions, like an employee call-off during a critical shift. Real-time insights enable managers to make compliant scheduling decisions fast, without compromising productivity or safety.
Future-Proofing Workforce Operations in Chemical Manufacturing
Keeping track of employee certifications, skills, and training can be overwhelming—especially across large, distributed teams. A centralized skills management system ensures that only properly trained individuals are scheduled for tasks involving hazardous materials or complex machinery.
With automated alerts for expiring certifications and built-in skill enforcement, chemical manufacturers reduce the risk of non-compliant task assignments and boost workforce readiness.
Regulatory compliance is more than just a checklist—it’s a culture. When employees know that rules are enforced fairly and consistently, it fosters accountability and trust.
Modern workforce management systems provide visibility into labor data across the organization, empowering frontline leaders to make informed decisions. By aligning staffing with both compliance and production goals, chemical manufacturers can create a safer, more engaged workforce.
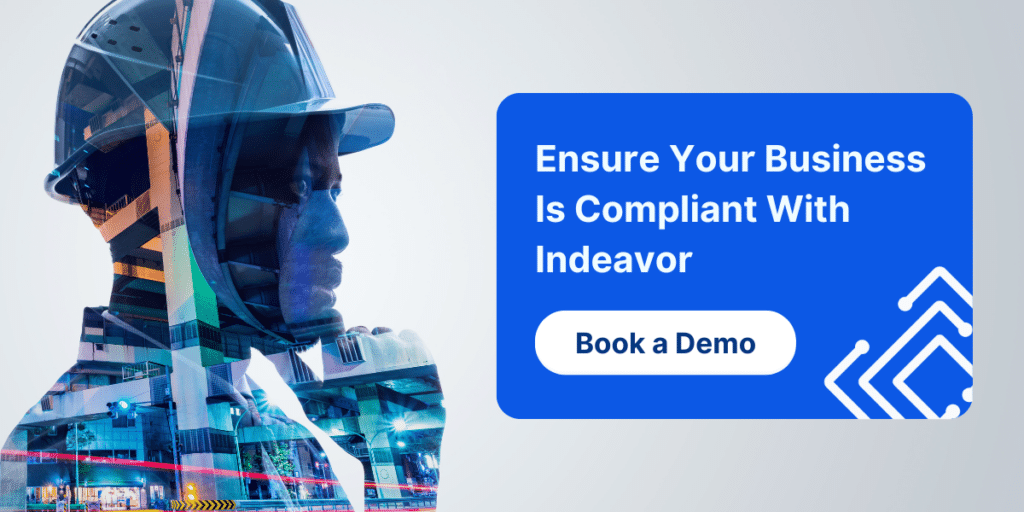
Why Indeavor is the Workforce Compliance Partner for Chemical Manufacturers
Indeavor’s workforce management platform is designed to meet the needs of highly regulated industries like chemical manufacturing. With advanced scheduling automation, real-time labor insights, and centralized skills management, Indeavor helps chemical manufacturers maintain compliance with confidence.
Whether you’re looking to improve labor cost control, reduce compliance risk, or enhance your readiness for audits, Indeavor provides the tools you need to modernize your workforce operations—without disrupting your existing workflows.
Our configurable platform supports your labor policies, tracks training and certification requirements, and generates the documentation necessary to prove compliance during regulatory reviews. Chemical manufacturers who partner with Indeavor experience improved workforce efficiency, fewer compliance headaches, and better operational outcomes.
Indeavor can help. Schedule a demo today to see how we empower chemical manufacturers to stay ahead of workforce regulations—with less stress and greater visibility.
About the Author
Claire Pieper is the Digital Marketing Specialist for Indeavor. In her role, she specializes in crafting strategic and engaging content, ensuring that customers are well-informed. Claire is dedicated to enhancing the customer experience and optimizing the user journey through Indeavor’s solutions. To learn more or get in touch, connect with Claire on LinkedIn.