Manufacturing is undergoing a digital transformation, and manufacturing leaders are stepping up to reimagine their operations from the ground up. At the heart of this transformation lies a powerful lever for competitive advantage: workforce strategy.
But what is a workforce strategy? It is the intentional design and alignment of labor resources to business goals—turning people planning into a proactive, strategic advantage. As labor shortages, increasing production demands, and global disruptions challenge traditional models, innovative manufacturers are rethinking how they attract, deploy, and retain talent.
From Fragmented to Integrated
For decades, manufacturers relied on manual processes and siloed systems to manage their workforce—spreadsheets for scheduling, whiteboards for shift swaps, and disconnected tools for tracking skills and compliance. But these outdated methods are no match for the complexity of modern manufacturing.
Leading manufacturers are adopting integrated workforce strategy platforms that centralize scheduling, compliance, and skills tracking. With real-time visibility into labor availability, qualifications, fatigue risk, and regulatory requirements, operations teams can make faster, data-driven decisions.
With integrated workforce strategy and planning, manufacturing leaders can:
- Forecast labor gaps in advance to prevent production delays.
- Automate shift assignments based on skills, certifications, and regulatory constraints.
- Align labor with machine availability, reducing costly downtime and boosting productivity.
- Track training and competencies to ensure employees are always qualified for the jobs they’re assigned.
Leveraging Technology
Technology transforms workforce strategy from a manual task into a data-powered function. Modern platforms use artificial intelligence and predictive modeling to anticipate labor demand, identify skills gaps, and surface scheduling conflicts before they cause disruption.
Digital scheduling tools, for example, enable scenario planning that accounts for fluctuating demand, employee preferences, and cross-training opportunities. Labor planning tools that integrate with MES and ERP platforms ensure your workforce is aligned with real-time production demands.
Some manufacturers are even implementing digital twins for labor planning—virtual models of the workforce that simulate the impact of various staffing decisions. These innovations allow operations leaders to test “what if” scenarios and optimize workforce deployment in real time.
People Are the Priority
While automation and data are essential to a strong workforce strategy, people remain at the core. Change management is a critical element of success—especially when introducing new systems and processes that impact frontline employees.
Manufacturers who lead through transformation are investing in transparent communication, intuitive user experiences, and mobile-friendly tools that empower employees. Providing visibility into their own schedules, offering flexibility, and recognizing skills development all contribute to greater engagement and retention.
Building a future-ready workforce doesn’t just mean plugging gaps—it means cultivating talent from within. Upskilling, cross-training, and competency tracking help manufacturers build resilience by ensuring employees are ready to take on new roles as the business evolves.
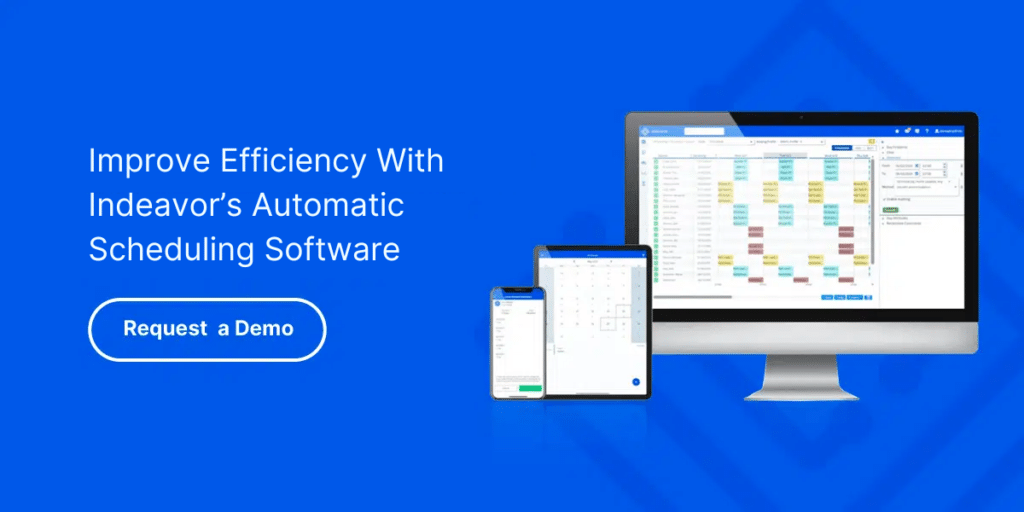
Workforce Innovation = Production Resilience
As supply chain volatility and labor constraints continue to challenge the industry, manufacturers with strong workforce strategies are proving more agile, responsive, and competitive.
According to Deloitte, 83% of manufacturing executives see labor shortages as their top concern. Those who invest in workforce innovation—combining technology with talent development—are better positioned to weather disruption and outperform their peers.
An effective workforce strategy ensures every shift is filled with the right people, at the right time, with the right qualifications. It minimizes downtime, supports compliance, and drives measurable business outcomes like reduced turnover, improved output, and lower labor costs.
The Competitive Advantage
With shrinking margins and rising expectations, workforce strategy has become a core pillar of competitive manufacturing operations.
Manufacturers that embrace modern workforce strategies:
- Build a culture of operational excellence.
- Enable data-informed decisions at every level.
- Enhance collaboration across HR, operations, and finance.
- Improve both employee experience and customer satisfaction.
The bottom line? Your people strategy is your business strategy.
The Path Forward
Now is the time to modernize your workforce strategy—before disruption forces your hand. Whether you’re upgrading legacy scheduling systems, investing in labor analytics, or rethinking how you support your frontline teams, the decisions you make today will define your success tomorrow.
Don’t wait for disruption to force change. Lead with intention, empower your workforce, and build a workforce management strategy that’s as agile and scalable as the products you create.
Ready to future-proof your operations? Book a demo to see how Indeavor can help you transform workforce strategy into a competitive advantage.