Manufacturing facilities, whether food processors or durable goods, have a bit of an overtime problem.
It’s easy to rely on overtime to meet the complex labor requirements of your SKUs. After all, front-line supervisors deal with tight production deadlines and overtime is typically guaranteed in union contracts anyway. Distributing OT hours can be critical to not just the health of your business, but also to increasing the satisfaction of your employees who depend on those extra hours.
There is such a thing, however, as “bad” overtime. Our newly released guide is here to help you discern between a positive OT process and a negative one.
You’ll learn 5 ways to scrutinize your current overtime processes along with tips to reduce overtime that’s hurting your bottom line.
A standardized overtime approval process provides visibility, mobile capabilities, and real-time information for those who need it most. Looking to ensure that your facility never schedules unnecessary overtime hours again and that needed hours are distributed fairly? Look no further than Indeavor.
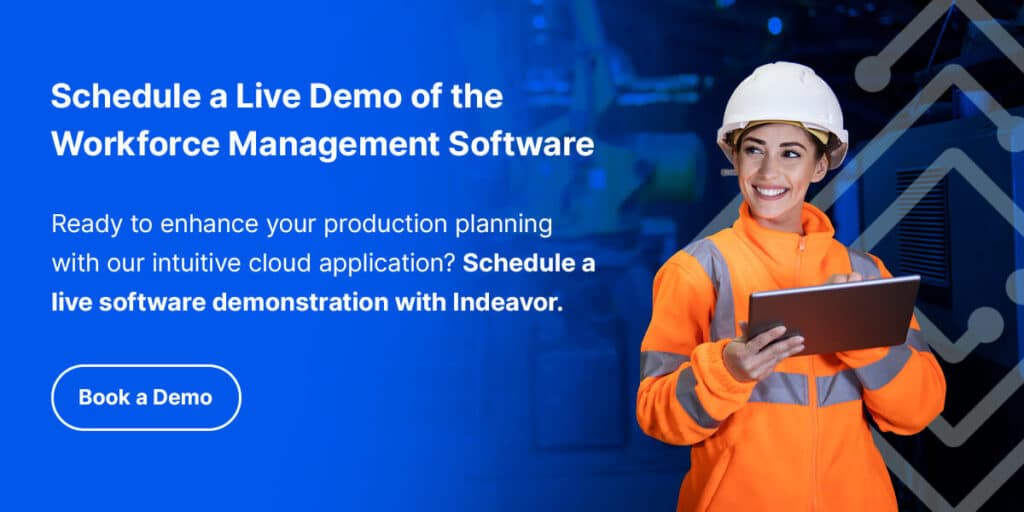
The Indeavor Solution
Your scheduling and overall workforce management processes can no longer rely on paper and outdated systems. To avoid audits and keep mandatory training and skills certifications in mind during scheduling, you need the cloud.
Indeavor’s solution offers clients an end-to-end, cloud-based employee scheduling and absence management system. By integrating with your human capital management and enterprise resource planning systems, you can leverage a robust platform that provides you with real-time employee data.
Relieve your supervisors of manual tasks and the constant mental fatigue brought upon by scheduling changes by automating the entire process, connecting the data to all of your existing corporate systems, and ensuring you always have the right qualified employee in each position.