We’ve discussed the origins of the American Petroleum Institute’s (API) RP 755, focusing on how the regulation is rooted in the need for updated scheduling practices.
The oil, gas, and energy sectors are among some of the few industries that have mandatory guidelines for fatigue management. While workers in any industry are susceptible to fatigue, the unique position of those who work at refining and petrochemical facilities puts them in more danger if they are not alert; they risk the wellbeing of themselves, their crew, and—in the event of an explosion or other disaster at the plant—entire neighborhoods.
So it’s no surprise that ‘Recommended Practice 755: Fatigue Risk Management Systems for Personnel in the Refining and Petrochemical Industries’ is getting an update with more stringent guidelines.
According to API, the primary focus of RP 755 is to “limit hours and days of work and address shift work”. The second edition is meant to further this standard.
For the oil and gas industry at large, that means that you have to deal with the dichotomy of operating within regulations and minimizing operational costs. While a difficult undertaking, it’s not impossible. The right automated scheduling solution can make it easy.
Updates From The API Press Release
A press release released by API earlier this month breaks down the changes to the original standard. The goal is to (1) reduce misunderstandings through more direct language and (2) avoid fatigue for all workers involved in safety-sensitive processes.
- Limits to Hours of Service: Updated guidelines applicable to all employees involved in process safety-sensitive actions, including how to manage call-outs (covered positions).
- New Guidance on the Work Environment: New requirements regarding lighting and fatigue assessment based on advances in the science since the first edition.
- Individual Risk Assessment and Mitigation: Highlights available technology that can detect fatigue, along with guidance on using objective, validated tools for assessing fatigue.
- “Shoulds” v. “Shalls”: Several sections were changed from “should perform” to “shall perform” to clarify that all components of Fatigue Risk Management Systems are needed, while still retaining flexibility in how they are implemented.
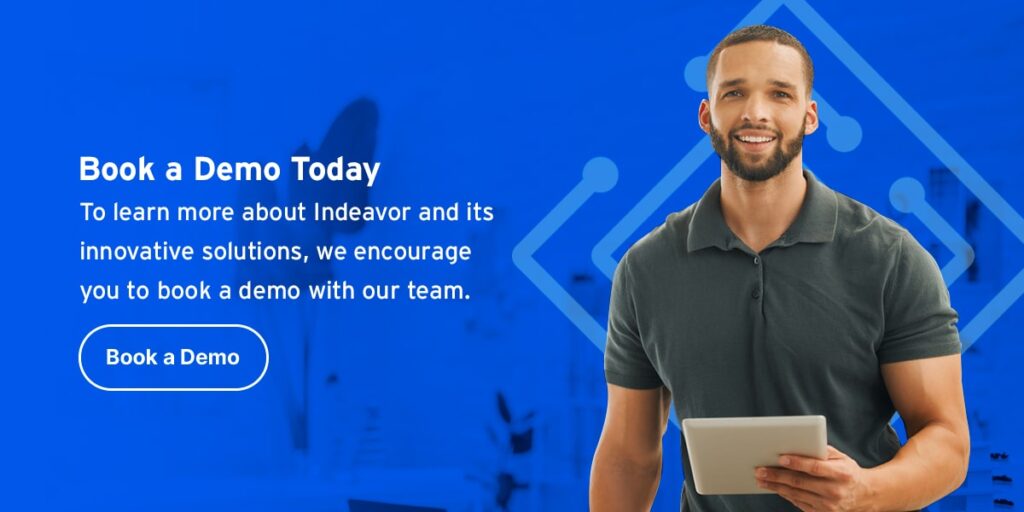
Challenges Facing the Petrochemical Manufacturing Industry
If you’re in petrochemical manufacturing, meeting each facility’s labor demands requires compliance management at the point of scheduling—beyond state labor laws and union agreements. They also need to take into account fatigue risk management, particularly the number of hours and days employees can work.
It’s incredibly difficult to track hours with paper schedules. Especially when changes are happening in real-time (shift swaps, absences, etc.) that do not get accounted for in the paper schedule—or T&A system.
Automated Scheduling Software for Manufacturing Plants
Here’s where Indeavor’s automated scheduling can help. Our configurable compliance rules, workflows, and reports can help manage and mitigate compliance concerns around the following ordinances: fatigue regulations, industry-standard best practices, federal and state work laws, and union rules.
By automating the 24/7 scheduling of plants enterprise-wide, you can more consistently enforce compliance. Without a centralized system like Indeavor, oil and gas companies are at a high risk of not being compliant with these specific rules; alternatively, they will spend a lot of time internally trying to manage them. Indeavor is your safety net because it automates this coverage.
Learn more or request a demo here.
Indeavor’s solution offers clients an end-to-end, cloud-based employee scheduling and absence management system. By integrating with your human capital management and enterprise resource planning systems, you can leverage a robust platform that provides you with real-time employee data. Relieve your supervisors of manual tasks and the constant mental fatigue brought upon by scheduling changes by automating the entire process, connecting the data to all of your existing corporate systems, and ensuring you always have the right qualified employee in each position.