Worker fatigue is often due to strenuous working conditions, long work hours, or an irregular work schedule. Due to being susceptible to all three, fatigue affects the majority (54%) of shift employees in the oil and gas industry. Drivers alone are 8.5 times more likely to die in a motor vehicle accident than those who work in other industries.
On March 23, 2005, the BP Texas City refinery experienced explosions that resulted in 15 deaths, over 180 injuries, and billions of dollars in damages. After two years of investigation, the Chemical Safety Board (CSB) ultimately discovered that operator fatigue played a role. Up until that day, the operators had been working 12-hour shifts for as many as 29 consecutive days.
This was the catalyst for Recommended Practice 755: Fatigue Risk Management Systems for Personnel in the Refining and Petrochemical Industries—or RP 755, for short.
We’ve discussed how automated scheduling can help the nuclear power industry combat its unique laws, particularly the fitness-for-duty programs outlined by the Nuclear Regulatory Commission. While those rules focus more on when an employee needs to have a break, RP 755 is dedicated to limiting hours and days of work.
Doing away with paper or excel and leveraging automated systems can help you more easily implement RP 755’s complex fatigue management rules into your scheduling process.
Hours of Service Guidelines
The Hours of Service guidelines break down the maximum number of shifts, maximum length of each shift, and the minimum time off after a work set for each shift pattern (12-hour, 10-hour, and 8-hour). For employees working 12-hour shifts, for example, they cannot exceed 7 consecutive shifts (day or night), need a minimum of 36 hours off after a work set, and can only work a maximum of 18 hours unscheduled.
That’s just for one shift pattern; that example doesn’t even dive into the different requirements for outages. Imagine trying to juggle these rules for each individual employee with paper processes.
It is both time-consuming and prone to human error, especially when managing hundreds (or thousands) of employees. Whether you’re unknowingly assigning an employee too many shifts in a row or providing too many overtime hours, an inefficient scheduling practice can lead to loss in productivity, failure to comply, or another preventable accident like BP’s.
Without a centralized system like Indeavor, oil and gas companies are at a high risk of not being compliant with these specific rules; alternatively, they will spend a lot of time internally trying to manage them. Indeavor is your safety net because it automates compliance coverage – union, local, state, federal, and fatigue.
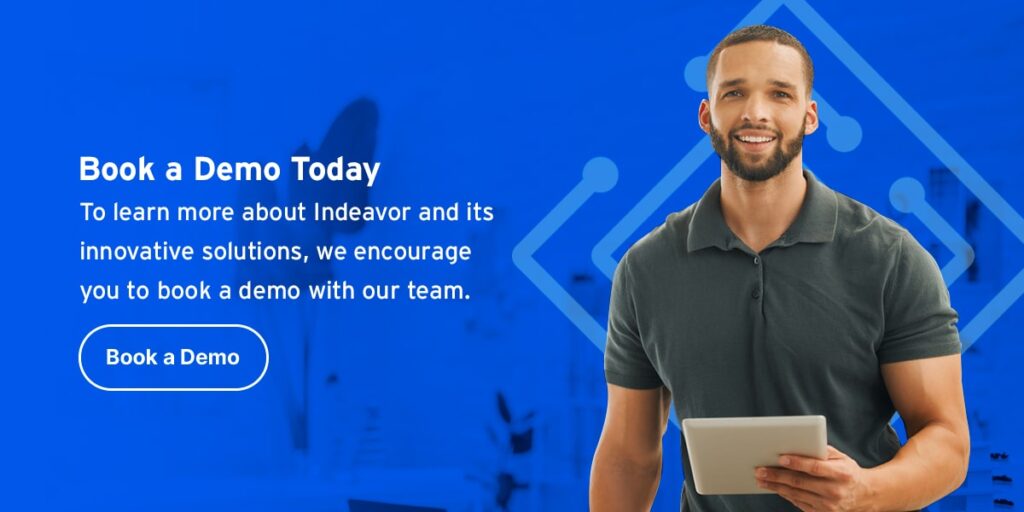
Oil & Gas Workforce Management With Indeavor
Indeavor is our workforce management SaaS solution which offers clients an end-to-end, cloud-based employee scheduling, time & attendance, and absence management system. Indeavor integrates with your human capital management and enterprise resource planning systems to create a robust platform that provides you with real-time employee data.
Learn more or request a demo.