In an era of increased work flexibility, one constant remains across the Industrial Enterprise – the need for people, 24/7, to deliver against increasingly volatile demands. Adding to this complexity, demands for products are rarely constant throughout the year. Especially in environments characterized by high-volume production (e.g., Consumer Packaged Goods).
Operators maintain several levers to combat these needs including:
- Increasing inventory
- Hiring temporary workers
- Leveling product mix between facilities
- Managing overtime
The most common lever is the use of overtime (OT). The concept is polarizing by itself as overtime is loved by some while others loathe the idea – especially when forced. Regardless of the workforce appetite, the use of overtime drives increased cost, impacts employee morale and drives additional complexity in the management of work rules.
And when a global labor shortage is coupled with volatile demands? More OT is forced, more people are stretched thin, increased cost per worker and increased risk of missed revenue due to missed production goals. How can operators most efficiently use overtime to optimize their P&L?
1. Maintain Direct Visibility of Demand Driven Staffing Needs
Most plant and facility leadership are in a state of “I’ll take whoever shows up” when it comes to labor staffing. Even in an environment where shift scheduling results in multiple gaps in assignments, operators must be intentional about staffing needs. This means only scheduling hourly employees against the demanded product.
This operational practice is a low investment in both resources and capital, with a major return. The foundational data structures of always maintaining staffing needs to demands will pay dividends when fully cost-optimizing your workforce planning efforts. Workforce scheduling software or other digital shift scheduling tools are purpose-built to always maintain visibility of staffing needs to demands.
2. Outline an Optimal Plan
Operators should intentionally remove the idea of “eliminating,” or even “reducing” overtime – the key being to “optimize” its use specific to your operating environment.
Overtime may be the most efficient way to meet the needs of a dynamic shift-driven environment. During these optimization efforts, it’s important to consider all critical inputs needed for scheduling hourly employees.
What are the needed skills/qualifications to meet demand?
What are the work rules that I must abide by?
Are grievances or compliance fees at risk with my strategy?
How does regularly scheduled time off impact my overtime strategy?
3. Understand Work Rules, and Give Teams the Tools to Support
Each operating environment is unique with rules governed by various drivers – industry, process, local, regional, union, work council, etc. Understanding these local rules at the leadership level is a “price of admission” to the role, but giving tools to all levels of the organization is critical to support appropriate decision-making. For example, a supervisor may have the autonomy to make an in-the-moment OT decision with major ripple effects – potentially resulting in a grievance, compliance fee, or employee moral impact.
Leveraging a platform with robust, rule-based building blocks can give all layers of the organization the confidence that the right decisions are being made at the right time.
4. Leverage Data to Drive Visibility
While data seems to drive every layer of the Industrial Enterprise, we are far from data-rich when it comes to the visibility of labor and associated costs. Defining key cost attributes aligned with labor is a simple, structured, and manageable way to promote the visibility of overtime usage that can be used to correlate against both cost & employee morale.
Much like we encourage our operating teams to ask “why,” we should do the same when managing our people:
- What are my standard reasons for overtime?
- Why was overtime used in this scenario?
- Why was this person, or group or people, leveraged?
System control of these variables can deliver differentiated operational maturity. Data add up quickly when we have a regular, system-driven cadence of collection.
5. Analyze, Improve, Repeat
Now that your data exists, return to the continuous improvement motions that differentiate our Industrial environments. Collect the data, analyze it, pareto the largest contributors, define action plans, Continuously Improve and Repeat.
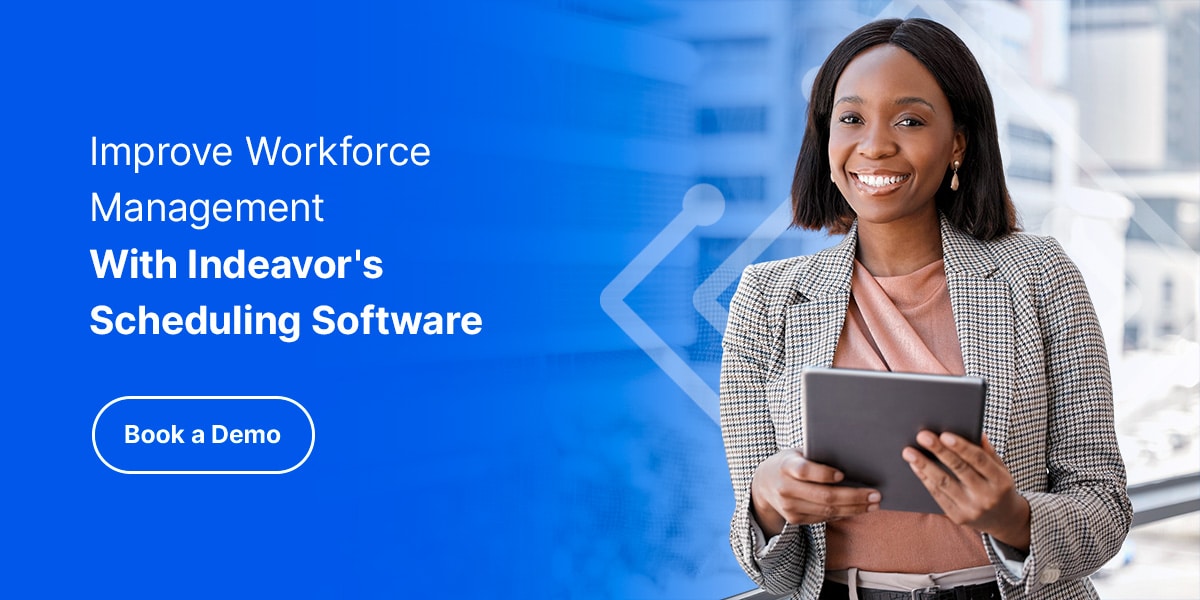
Manage Overtime with Indeavor’s Workforce Optimization Solutions
Did you know that with Indeavor’s shift scheduling and optimization solution, the average savings on labor costs is 3 – 8% annually? One of our clients shared that their savings are closer to 12% of overall labor costs. With structured system-driven methodology and governance, you can achieve sustainable, material benefits across your facility and your enterprise network, including:
- Specified labor allocation standards
- Visibility into cost variability (OT, Direct vs. Indirect, Skills, and more)
- Reduction of grievances, enhancement to the employee experience and overall improvement of productivity
- Proprietary facility workforce analytics to improve strategic and tactical operation efforts
To speak with one of our workforce management experts or request a complimentary consultation, email our team at sales@indeavor.com and someone will reach out shortly.
About the Author
Bradley Jones leverages his Manufacturing Technology and Operations background to serve the Global Indeavor consumer base. To learn more or get in touch, connect with Brad on LinkedIn.