The industrial sector is changing quickly, and it is important for companies in this space to make sure that they have a wide variety of versatile, adaptable systems that can adjust depending on the work environment. Transparency and visibility are critical, and facilities must continually re-evaluate the data to make sure they are getting the most out of their internal systems. Why is it vital for industrial organizations to invest in an adaptable system, and what are the benefits of connecting them together?
Use Data to Craft a More Resilient Supply Chain
One of the biggest reasons why industrial organizations need to invest in adaptable, connected systems is that they can use this information to build a more resilient supply chain. Today, there are a lot of supply chain difficulties, and a lot of companies rely on multiple suppliers for various aspects of their inventory. That way, if one supplier has a problem, they can simply lean on the other suppliers to pick up the slack.
At the same time, this means that manufacturers and other industrial facilities need to be able to adjust quickly. If customers come with a production shift, change, or increase, they need to use their connected systems to adjust, adapt, and deliver the new order as quickly as possible. Having a connected system makes this process far easier than clunky and cumbersome paper workflows.
Managing production and shift scheduling in Excel spreadsheets wastes thousands of hours, year over year, causing a leak in the enterprise and is also prone to expensive errors. Transitioning to digital workflows has been proven to promote worker safety while boosting productivity.
Build a Strategy for Connected Products
Industrial organizations also need to explore ways to create an innovative, connected ecosystem. Some of the benefits of connecting multiple components together include:
- With highly connected and modular components, industrial companies can adapt to continuously changing circumstances.
- Organizations can take advantage of automation technology, which will make it easier to meet deadlines while matching production to demand.
- A connected ecosystem makes it easier to analyze detailed performance information, allowing organizations to make changes in the process as needed.
- Connected products provide access to real-time information that can be aggregated to design products and services better.
The biggest and best way to boost productivity and control costs is to access visibility into the workforce via connected applications. Connecting the data from HCM, ERP, T&A, and LMS technology via an integrated workforce management platform allows operations to trend workforce data to make better decisions. Furthermore, having an integration with an ERP system into and intelligent workforce management system will allow organizations to automatically schedule labor to match changing demands in the ERP, taking enterprise automation and workforce optimization to the next level. For all of these reasons, organizations need to invest in an ecosystem of connected products that can help them stay one step ahead of the other companies in the field.
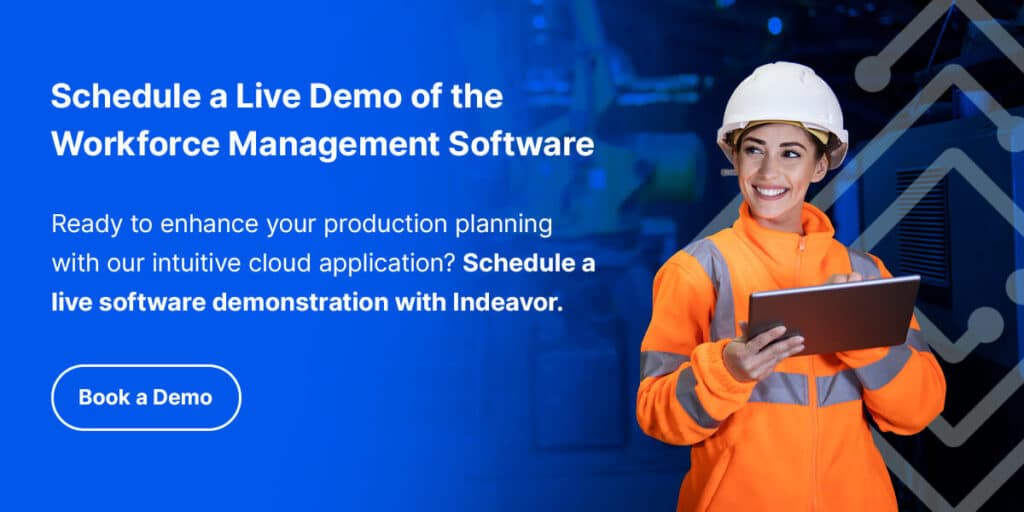
The Importance of Data Accessibility and Visibility in Operations
Above all else, industrial organizations need to make sure that they prioritize data accessibility and visibility. It is a critical part of workforce optimization, and it can make a significant difference in helping companies optimize their resources.
This information can be used to save time and energy that is otherwise wasted on outdated processes, and organizations can use this information to deliver rules-driven, intelligent automation. With access to unified, accurate data, it is much easier for manufacturing companies to ensure all proper workforce management practices are followed and that resources are being used wisely.
Indeavor Connects the Dots to Your Industrial Operations Ecosystem
It is important for organizations to make sure they are properly leveraging all of their resources, and this includes their most important asset—their skilled workers. With Indeavor, companies get access to detailed people analytics that they can use to implement employee scheduling technology. By making shift scheduling easier, businesses can optimize their labor analytics, making sure all of their employees are being put in the best position possible to be successful. You can also use automated scheduling practices to improve employee satisfaction, which can optimize your retention rate. If you would like to learn more about how we can help you get the most out of your workforce, contact us today!