In the food processing industry, labor reliability isn’t just important—it’s foundational. With tight production windows, strict regulatory oversight, and demand that shifts daily, food manufacturers must rethink how they build and support their teams with visionary workforce strategies.
Labor shortages are mounting across the supply chain, and food manufacturing is no exception. According to the Manufacturers Alliance, the average turnover rate in the manufacturing sector reached 39% in 2022, highlighting a growing need for talent retention and workforce stability. At the same time, organizations are juggling evolving health standards like FSMA and OSHA requirements.
This pressure is prompting forward-thinking companies to embrace transformative strategies that prioritize both operational agility and employee well-being. That’s where modern workforce strategies come in. The future of the industry depends on an adaptable workforce facing strategies that support compliance while reducing turnover and boosting productivity.
The Visionary Mindset: Empowerment
Forward-thinking food processors are replacing static schedules with flexible, scalable workforce strategies that adapt to both operational and employee needs. Here’s how:
- Dynamic Shift Scheduling: reduce repetitive strain injuries and helps prevent fatigue by rotating duties and optimizing time off.
- Real-Time Communication Tools: ensure employees receive last-minute shift updates, weather alerts, or safety notices instantly.
- Demand-Driven Labor Forecasting: use historical and real-time production data to schedule only the staff needed, reducing unnecessary labor costs without risking understaffing.
These workforce strategies not only improve agility—they also foster a culture where employees feel valued, informed, and supported.
Case in Point: Measurable Benefits
Organizations that integrate modern workforce strategies are unlocking new levels of agility and resilience. Consider how a few segments of the food industry are seeing measurable benefits:
- Dairy processing operations can use scheduling analytics to prevent understaffing during production peaks, increasing output with no additional hires.
- Frozen foods manufacturers have the ability to reduce turnover by aligning shifts with employee preferences, boosting efficiency.
- Organic food packaging facilities utilizing integrated digital time tracking and fatigue monitoring improves USDA compliance audits and worker satisfaction.
Each of these examples demonstrates the power of a modern workforce management solution tailored to the unique challenges of food processing. By prioritizing flexibility, compliance, and employee well-being, food manufacturers can drive sustainable success in an increasingly competitive market.
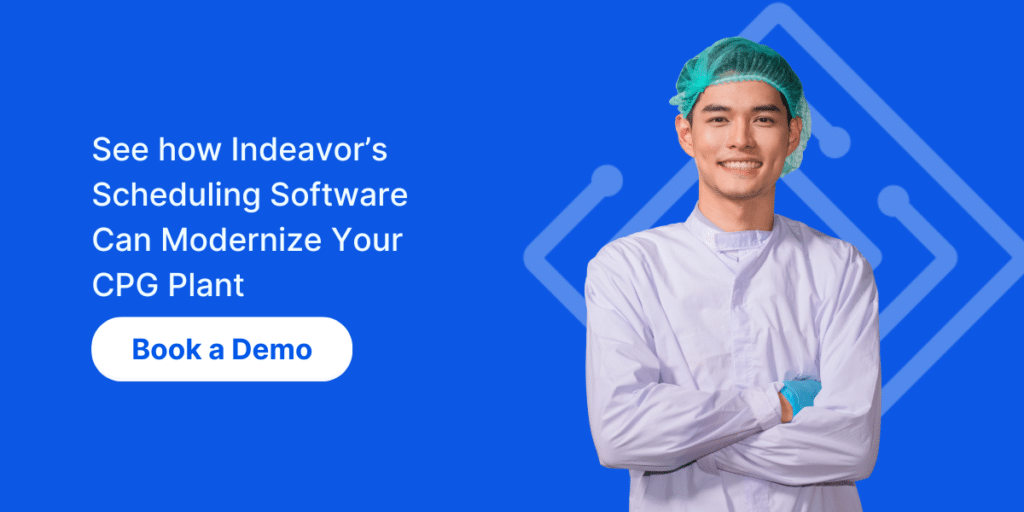
Purpose-Driven Workforce Models
The most impactful labor strategies go beyond day-to-day operations—they shape your employer brand and workplace culture. In a tight labor market, reputation matters. Facilities that offer predictable schedules, fair treatment, and safety-focused environments are winning the competition for talent.
Food processors are redefining what it means to be a great place to work by:
- Offering flexible shift options that accommodate work-life balance.
- Implementing inclusive policies to attract a broader talent pool.
- Using scheduling data to avoid burnout and boost team morale.
These strategies aren’t just good for the bottom line—they create workplaces where people want to stay and grow. And that long-term loyalty is critical in an industry with historically high churn.
Take the First Step Toward Future-Ready Operations
Smart workforce strategies begin with a clear-eyed view of your current workforce management systems. Are your scheduling practices reactive or proactive? Do your employees feel informed and empowered? Can you confidently meet compliance requirements at a moment’s notice?
Whether your goal is to reduce turnover, meet compliance demands, or improve operational flow, modern workforce planning can uncover untapped performance across your facility. Effective workforce strategies also help future-proof operations against labor shortages and regulatory changes. Organizations that invest in smarter scheduling and communication tools today will be better positioned to scale and adapt tomorrow.
We’re not just feeding communities—we’re feeding a smarter, more human-centered way to work. Don’t just meet today’s expectations. Book a demo to see how modern workforce management can help you build the labor model that fuels tomorrow’s success.