Organizations are constantly seeking ways to enhance efficiency, optimize processes, and maximize productivity. One methodology that has gained widespread recognition for achieving these goals is Lean Manufacturing. In this article, we delve into the fundamentals of Lean Manufacturing, exploring its key principles and the significant benefits it offers for workforce management.
Core Principles of Lean Manufacturing
Originating from Toyota’s renowned Toyota Production System (TPS) in the 1950s, Lean Manufacturing has evolved into a comprehensive approach aimed at minimizing waste while maximizing value. At its core are several fundamental principles:
Just-in-Time (JIT) Production
A core principle of Lean Manufacturing revolutionizes traditional production methods by emphasizing the production of goods or services only as needed, precisely when they are needed. This approach minimizes the accumulation of excess inventory, thereby reducing storage costs and the risk of obsolescence.
By synchronizing production with customer demand, JIT enables companies to operate with leaner inventories while ensuring timely delivery to customers. This not only optimizes resource utilization but also enhances responsiveness to changing market demands, ultimately improving overall operational efficiency and customer satisfaction.
Continuous Improvement (Kaizen)
Kaizen embodies the philosophy of continuous, incremental improvement in all aspects of an organization’s operations. It encourages employees at all levels to actively participate in identifying inefficiencies, brainstorming solutions, and implementing small, iterative changes to enhance processes continually.
By fostering a culture of experimentation, learning, and adaptation, Kaizen drives sustainable improvements in quality, efficiency, and customer satisfaction over time. This approach empowers employees to take ownership of their work, driving innovation and fostering a sense of pride and engagement within the organization.
Respect for People
Central to Lean Manufacturing is the principle of respecting people, and recognizing that employees are the most valuable asset of any organization. This principle entails creating a work environment that values and supports employees’ well-being, growth, and involvement in decision-making processes.
Organizations that prioritize respect for people invest in employee training and development, provide opportunities for career advancement, and cultivate open communication channels. By fostering a culture of trust, collaboration, and mutual respect, companies can harness the full potential of their workforce, driving innovation, and achieving superior performance.
Elimination of Waste
Waste is any activity or process that does not add value to the final product or service from the customer’s perspective. Lean Manufacturing aims to eliminate waste in all its forms, including overproduction, waiting time, unnecessary transportation, excess inventory, defects, overprocessing, motion, and underutilized talent.
By identifying and eliminating waste throughout the value stream, organizations can streamline operations, reduce costs, and improve efficiency. This not only enhances the value delivered to customers but also creates a more sustainable and environmentally friendly business model.
Value Stream Mapping
Value Stream Mapping (VSM) is a powerful visual tool used to analyze, understand, and improve the flow of materials and information required to deliver a product or service to customers. By mapping the entire value stream from raw materials to the end customer, organizations can identify value-added and non-value-added activities, as well as bottlenecks and inefficiencies.
This enables companies to streamline processes, reduce lead times, and eliminate waste, ultimately improving overall operational performance and customer satisfaction. VSM serves as a roadmap for continuous improvement initiatives, guiding organizations toward their goals of delivering greater value with fewer resources.

Key Benefits of Lean Manufacturing in Workforce Management
Implementing Lean Manufacturing principles in workforce management yields numerous benefits, including:
- Improved Efficiency and Productivity: By eliminating waste and optimizing processes, Lean facilitates smoother operations, leading to increased productivity.
- Enhanced Quality Control: Lean emphasizes defect prevention and quality at the source, resulting in higher-quality products or services and reduced rework.
- Reduction of Wasteful Activities: Lean methodologies target waste across all facets of operations, leading to resource optimization and cost savings.
- Empowerment of Employees: Lean encourages employee involvement and empowerment, leading to higher morale, greater job satisfaction, and increased innovation.
- Adaptability and Flexibility in Operations: Lean organizations are more agile and responsive to changing market conditions, enabling them to adapt quickly to customer demands.
- Cost Reduction and Profitability: By minimizing waste and improving efficiency, Lean reduces operating costs and enhances profitability.
- Enhanced Customer Satisfaction: Lean’s focus on delivering value to the customer results in higher customer satisfaction levels and fosters long-term customer loyalty.
According to a study by the Lean Enterprise Research Centre (LERC) at Cardiff University, organizations that have successfully implemented Lean Manufacturing principles have reported an average increase in productivity ranging from 10% to 30%. This significant improvement in productivity underscores the effectiveness of Lean methodologies in optimizing operations and streamlining workforce management practices.
Implementing Lean Principles in Workforce Management
Implementing Lean principles in workforce management is essential for organizations striving for operational excellence and continuous improvement. This excerpt highlights key strategies for integrating Lean methodologies into workforce management practices, emphasizing the critical role of leadership commitment, employee involvement, performance measurement, continuous monitoring, and the integration of Lean tools and techniques. By embracing these principles, organizations can optimize processes, enhance productivity, and foster a culture of innovation and excellence throughout the workforce.
Leadership Commitment and Vision
Successful implementation of Lean principles in workforce management requires unwavering commitment and vision from organizational leaders. Leaders must articulate a clear vision for adopting Lean practices and demonstrate their commitment through actions and behaviors. They play a crucial role in setting strategic objectives, allocating resources, and providing direction and support throughout the implementation process. Leadership commitment creates a sense of urgency and accountability, inspiring employees to embrace change and actively participate in Lean initiatives.
Employee Training and Involvement
Employee training and involvement are essential components of implementing Lean principles in workforce management. Comprehensive training programs ensure that employees understand Lean concepts, methodologies, and tools, empowering them to contribute effectively to process improvement efforts.
Additionally, involving employees in the implementation process fosters a sense of ownership and commitment to change. Organizations should provide opportunities for employees to participate in problem-solving teams, kaizen events, and other continuous improvement activities, encouraging collaboration and innovation at all levels.
Establishment of Key Performance Indicators (KPIs)
To measure the effectiveness of Lean initiatives in workforce management, organizations must establish Key Performance Indicators (KPIs) aligned with strategic objectives. KPIs provide quantifiable metrics for evaluating performance, tracking progress, and identifying areas for improvement.
Examples of KPIs in Lean workforce management may include productivity metrics, quality indicators, lead times, employee engagement scores, and customer satisfaction ratings. By establishing clear KPIs, organizations can monitor the impact of Lean practices on business outcomes and make data-driven decisions to drive continuous improvement.
Continuous Monitoring and Improvement
Continuous monitoring and improvement are fundamental principles of Lean management. Organizations must establish systems and processes for ongoing monitoring of performance against established KPIs, as well as feedback mechanisms for soliciting input from employees and stakeholders.
Regular reviews and audits help identify deviations from targets and opportunities for optimization. Continuous improvement involves identifying the root causes of issues, implementing corrective actions, and striving for incremental enhancements in processes, systems, and behaviors. By embracing a culture of continuous learning and adaptation, organizations can sustain momentum and drive long-term success.
Integration of Lean Tools and Techniques
Integrating Lean tools and techniques into workforce management processes is essential for maximizing efficiency and effectiveness. Organizations can leverage tools such as 5S, kanban, standardized work, visual management, and root cause analysis to streamline operations, reduce waste, and improve productivity. Additionally, Lean principles can inform decision-making in areas such as workforce planning, resource allocation, performance management, and talent development. By embedding Lean principles into day-to-day operations, organizations can create a culture of excellence and drive sustainable improvements in workforce management.
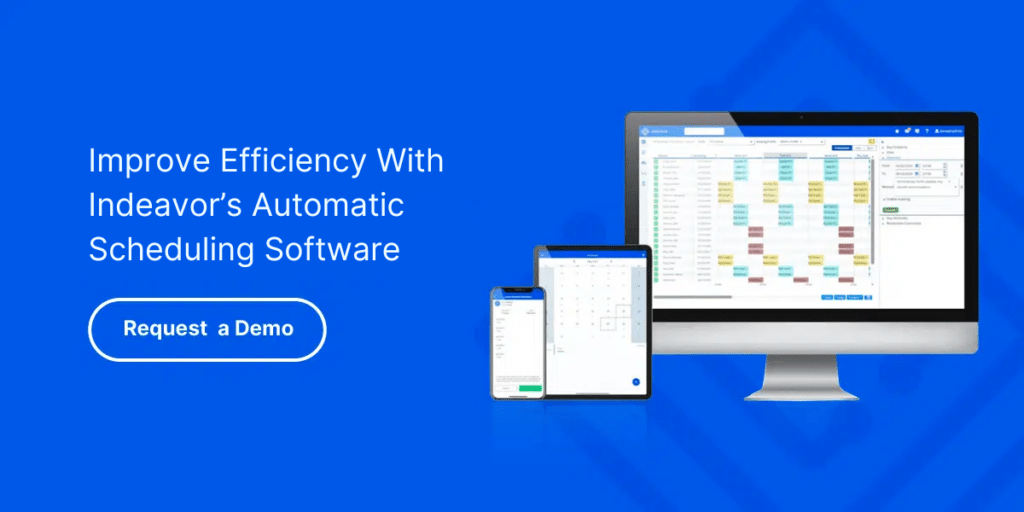
Challenges and Considerations
Navigating through organizational change can be a daunting task, especially when introducing Lean principles into workforce management. That’s why it’s important to understand common hurdles encountered during this transformational journey and offer insights into overcoming them. From resistance to change stemming from fear and uncertainty to cultural and organizational barriers hindering progress, organizations face multifaceted challenges.
However, by implementing effective change management strategies, addressing cultural impediments, and fostering a culture of continuous improvement, organizations can overcome these obstacles and sustain Lean practices for long-term success in workforce management.
Resistance to Change
Resistance to change is a common challenge encountered when implementing Lean principles in workforce management. Employees may resist changes to established processes, routines, and job roles due to fear of the unknown, perceived threats to job security, or skepticism about the benefits of Lean initiatives. Effective change management strategies, including communication, education, involvement, and support, are essential for overcoming resistance and building buy-in among employees.
Cultural and Organizational Barriers
Cultural and organizational barriers can hinder the successful implementation of Lean principles in workforce management. Factors such as hierarchical structures, siloed departments, lack of collaboration, and resistance to sharing information may impede progress. Organizations must address cultural and organizational barriers by promoting transparency, fostering teamwork and collaboration, breaking down silos, and aligning incentives and rewards with Lean objectives.
Sustaining Lean Practices Over Time
Sustaining Lean practices over time requires ongoing commitment, discipline, and reinforcement. Organizations must guard against complacency and ensure that Lean principles become ingrained in the organization’s DNA. This involves fostering a culture of continuous improvement, providing ongoing training and development opportunities, celebrating successes, and recognizing and rewarding employees for their contributions to Lean initiatives.
Additionally, organizations must remain vigilant in monitoring performance, identifying emerging issues, and adapting Lean practices to evolving business needs and external conditions. By nurturing a culture of resilience and adaptability, organizations can sustain Lean practices over the long term and realize lasting benefits in workforce management.
Conclusion
Lean Manufacturing offers a powerful framework for optimizing operations and enhancing workforce management. By embracing Lean principles, organizations can achieve greater efficiency, higher quality, and improved customer satisfaction. As businesses strive for excellence in today’s competitive environment, Lean Manufacturing remains a cornerstone for success.
If you’re interested in implementing a workforce management solution, consider exploring Indeavor’s solutions. Our comprehensive workforce management software is designed to support Lean practices and drive operational excellence. Book a demo today to learn more about how Indeavor can help transform your organization
About the Author
Claire Pieper is the Marketing Communications Coordinator for Indeavor. In her role, she specializes in crafting strategic and engaging content, ensuring that customers are well-informed. Claire is dedicated to enhancing the customer experience and optimizing the user journey through Indeavor’s solutions. To learn more or get in touch, connect with Claire on LinkedIn.