Higher input costs are pressuring U.S. food companies to raise prices in 2019, as the cost of production is growing at a faster rate than consumer prices. Employee scheduling practices can help you reduce your consumer costs.
With consumers already quite comfortable after years of low household inflation, is risking resentment by passing costs on to consumers to protect profit margins worth it?
Some certainly seem to think so—mainly due to transportation becoming a lot more expensive. Driver shortages, increased fuel prices, and raising pay to retain drivers all contribute to the rising freight expenses that have been sending shockwaves throughout the industry.
While transportation costs are out of your facility’s control, there is another factor contributing to the costs incurred during production that you can control: your own labor pool.
We’ve discussed how your workforce is your biggest expense each month and how an automated scheduling solution can help trim costs. Let’s dig deeper and pinpoint how strategic scheduling can help offset those uncontrollable increases in your input costs, making price hikes unnecessary (and giving you a competitive advantage).
1. Match Labor with Production Demand
Inaccurate forecasting negatively impacts the bottom line. If you have too many employees scheduled at the plant, you’re stuck paying for redundancies. If you don’t have enough people to get the job done, you need to assign more overtime hours or risk halting production—more on that below.
Wouldn’t it be nice if you could ensure that your positions are never understaffed or oversubscribed again?
With real-time analytics to determine demand, you can!
When the scheduler is able to quickly assess what their spread looks like, they can proactively control for any gaps. Real-time updates make it easier to determine when it’s time to schedule overtime for qualified employees, bring on temp workers, or relieve a few people from their shifts. All of this will save you much-needed dollars because schedulers and demand planners will only be creating rosters that fit your facility’s current, actual need.
That’s probably why 52% of organizations surveyed by Aberdeen claimed a top workforce management pressure was better access to workforce data to improve decision-making.
Speaking of decision-making…
2. Monitor Overtime Hours
When managers and schedulers cannot accurately anticipate their overtime costs, organizations find themselves hemorrhaging money very quickly on unnecessary overtime.
In the same Aberdeen study, automated workforce management solutions were shown to reduce unplanned overtime; those without automated scheduling consider about 27% of their overtime budget to be unplanned, while those leveraging automation only incur less than 4% of unbudgeted overtime.
One way to increase employee scheduling practices is with an automated scheduling solution. This can allow you to input company restrictions based on your specific business needs. Each shift employee will be assessed by these pre-determined rules when the schedule automatically generates, guaranteeing that managers won’t be blindsided by any overtime hours clocked in.
The decision-making is essentially done for you.
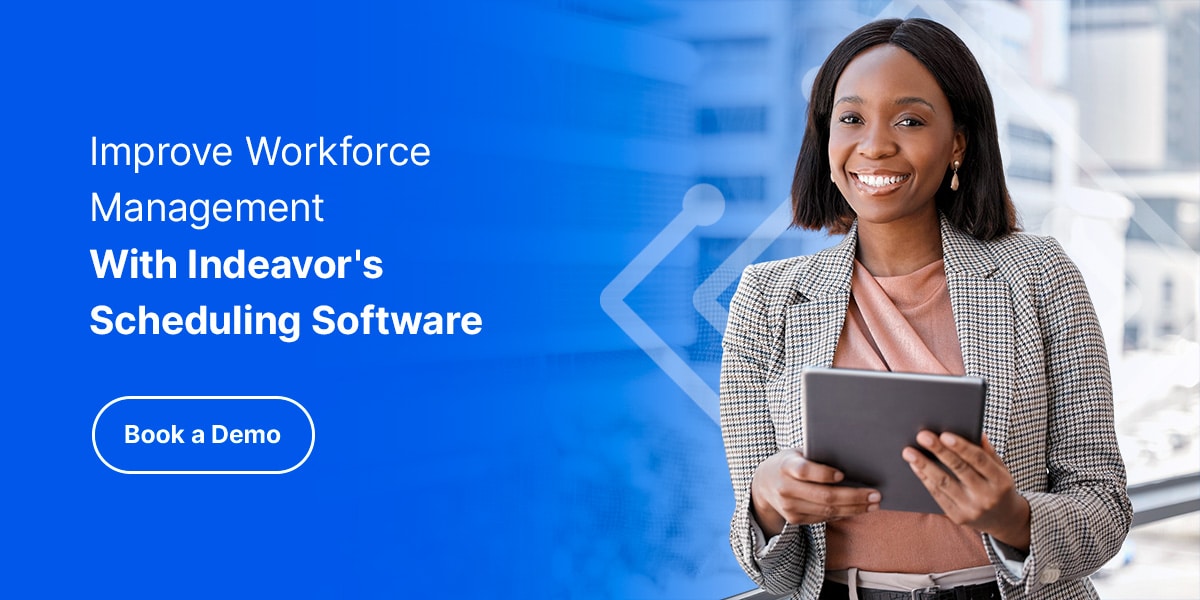
3. Avoid Non-Compliance Fines
Perhaps the most avoidable (yet damaging) costs are fines for non-compliance, from union grievances to failing to adhere to FSMA laws.
It seems simple enough: remain complaint and you’ll have nothing to worry about.
But as a food processor, you know that is easier said than done. You belong to one of the most heavily regulated industries in the country and for good reason. Human error in food manufacturing is a public health issue, as contamination can cause illness and death.
To stay compliant, only workers with the right certifications should be scheduled for specific tasks. It’s easy to lose track of employee qualifications and certifications, however, when you host all your employee information in an Excel spreadsheet or across scattered piles of paper.
To handle the complexity, you’ll need a fully functional and integrated qualification management system (QMS) that automatically breaks down the skills across your entire workforce and allocates the right person for the job. Schedulers can ensure that they assign the most qualified workers to each position at the click of a button. They can even search and identify the most optimal employees for the shift based on specific skills certifications.
Qualification mapping happens during the scheduling process in minutes, mitigating the risk of an unqualified worker being on the line, which in turn mitigates the risk of unnecessary fines.
Improve Your Employee Scheduling Practices With Indeavor
our workforce management SaaS solution which offers clients an end-to-end, cloud-based employee scheduling, time & attendance, and absence management system. Looking to control labor costs so you can avoid price hikes and keep loyal consumers happy? Indeavor is here to help.
Click here to request a demo.