Your shift begins in five minutes, critical assets are scheduled to run, absenteeism is as high as it has ever been and you know the key to a safe, productive, and quality-focused day means a successful start.
Does this scenario sound like your operating reality? If so, you are like the hundreds of discrete manufacturers we talk with regularly who are balancing supply chain volatility, labor shortages, and lofty KPIs with increased product complexity and cost competition.
The ability to ensure a consistent shift hand-off and protect the first hour of production, your Golden Hour, is critical to achieving your shift production goals where any productivity issues may end up rippling through your daily, weekly, and monthly targets. This consistency works both ways, I still have the memory of my first plant manager drilling in the idea that “stops breed stops,” meaning the asset/machine/process wants to run – it’s up to you to support its success.
The most immediate way to enable a consistent Golden Hour is to ensure a well-defined Labor Strategy and Staffing Plan aligned with the required versatility/skills, demand priorities, and complex labor rules (union contracts, compliance requirements, etc.). When that Staffing Plan inevitably requires a reactive adjustment, make sure the appropriate solutions are in place to effectively do so.
Hope is not a strategy and an undefined reaction is not a plan. So how can you provide the people in your manufacturing organization the solutions to achieve Golden Hour consistently?
1. Operate at the Right Level of Your Manufacturing Organization
There is a reason companies invest heavily in operational excellence to eliminate waste, improve quality and reduce costs – it works. Material results can be achieved with the right standards, operating cadence and mindsets. One defining component of any such program is operating at the right level for your organization.
This means decision-making closest to the action allows operators to produce, supervisors to improve, leaders to plan and executives to drive strategy. Without the right focus, this can quickly become a filed-away standard instead of an operating practice.
The first hour of production should be an event. Those closest to delivering production (Operators and Supervisors) must be enabled by all departments. As said across disciplines, over-planned initiation leads to consistent and streamlined results.
In parallel with questioning output, leaders should invest time in the feedback loop to support a successful start-up. They must understand this cadence, drive the over-planning required for consistent success, and most importantly provide the required tools for success.
2. Measure Granular Results
What level is your organization tracking throughput? The common view across global manufacturers is a metric-driven Obeya room outlining key performance indicators, Kaizen activities, and other value-driving initiatives. In most processes, there remains an opportunity to drive this tracking to a more granular level to enable Golden Hour throughput.
What is output for the first hour? What is the associated downtime during shift transitions? Based on Pareto-driven analysis, what initiatives can we drive to realize improvements?
Too often we will assume throughput is hindered by uncontrolled or investment-heavy causal factors – granular analysis often provides more visibility into controllable activities like staffing gaps, inopportune changeovers, or inventory shortages at any point in the value stream.
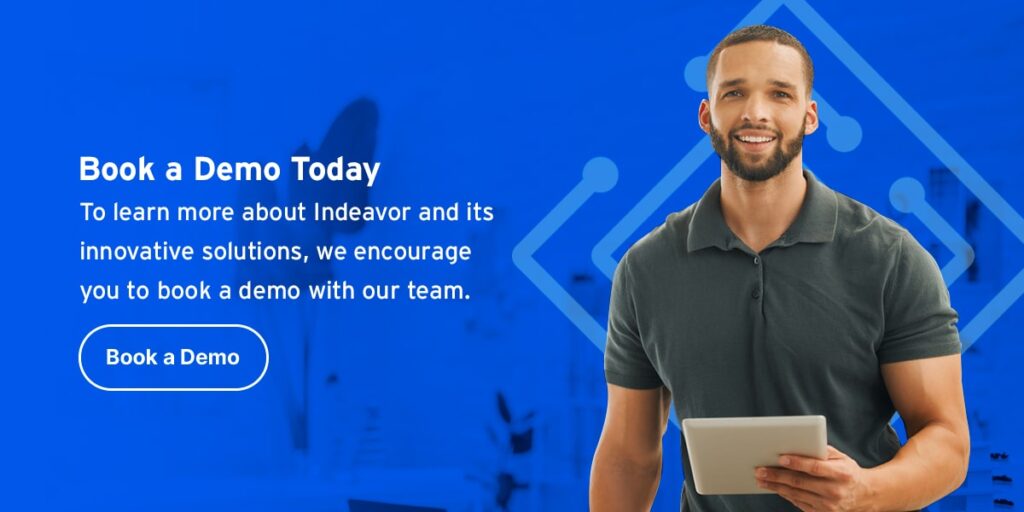
3. Manage Employee Skills at the Point of Assignments
Ensuring the appropriate training for employees prior to initiating production is critical to all manufacturing processes. How this data is maintained, shared, and incorporated into the operating cadence is pure opportunity. While tools are present, both application-based and manual systems, most manufacturers are managing skills/versatility inefficiently – specifically at the point of assigning work.
As product complexity increases and new technology is introduced, skills management will have a significant impact on a manufacturer’s profitability. Today, companies are investing millions to build skills-rich candidate pipelines in key geographies. This focus must be incorporated into the shop floor.
Two scenarios make up a majority of the operating inefficiencies:
- A Supervisor must manually assess if an operator has the appropriate training prior to assigning work.
- Knowledge of skills or qualifications is maintained in the Supervisor’s mind as legacy knowledge.
Facilities can “get by” with the above in a world with no volatility. In the operating reality, it becomes critical to avoid repeating inefficient processes and align skills at the point of assignments.
4. Optimize Your Operating Ecosystem
Labor analytics within a connected application ecosystem will become a “price of admission” for the factory of the future. The ability to seamlessly see the impact of labor on the financial, quality, productivity and cultural drivers of your business will be key to navigating increased complexity.
To begin your journey of data visibility, start with the fundamentals:
- Are your demands integrated directly with financially driven labor allocation standards?
- Is there a seamless reconciliation of actual employee schedules (inclusive of labor rules) within your time management system?
- Can your employees take accountability of their schedules, leave balances and team environment from the palm of their hand?
If you answered no to any of the above, you’re behind the curve. Modern-day technology makes this a reality beyond the speed and capability of internal teams.
5. Invest in an Automated Labor Scheduling Software
While our industry races towards digital transformation, it remains clear that people – from Operator to Plant Manager – are critical to execution and leveraging data to drive improvements. Your labor force and production requirements are a symbiotic relationship requiring constant alignment.
The majority of manufacturing facilities leverage manual spreadsheets, custom (legacy) database queries, and paper to maintain this critical connection. Like the digital tools that are re-inventing the factory of tomorrow, leveraging a best-in-breed automated employee scheduling solution provides the visibility, automation and accuracy required to achieve scalable ROI.
Are you still trying to gain an understanding of how these solutions drive value? Ask yourself these key questions:
- Do my Supervisors and Operations leaders spend hours aligning a schedule to demands?
- Are overtime costs rising with limited visibility of how to improve?
- Are grievance costs accepted as a “price of doing business” within your organization?
- Does labor data, aligned with demands drive daily decision-making? Is this data easy to compile?
- Is there a lack of alignment between time, attendance, payroll and scheduling processes?
If you answered yes to any of the above, you are not alone. Leveraging these tools can automate hours of supervisor work, reduce errors, provide visibility of key data and eliminate grievances/compliance breaches through rule-driven automation.
The result? Happier employees, cost avoidance and increased production output – starting with your Golden Hour.
Optimize Discrete Manufacturing Processes During the Golden Hour
If you want to maximize throughput, you must be relentless about your Golden Hour. This requires the right people, processes and technology.
- Operate at the right level of your organization to fuel your process and production demands.
- Measure granular results to tactically understand your opportunity and react with the highest level of detail.
- Manage employee skills at the point of assignment and streamline workforce allocation through system-driven skills management.
- Optimize your operating ecosystem by leveraging robust labor and people analytics to drive macro-level visibility.
- Invest in an automated labor scheduling solution and leverage experts to enable systems to solve key business problems.
Ready to take control of the golden hour and maximize your throughput?
Contact the workforce management experts at Indeavor today for a demo of the automated scheduling system used by over 100,000 users worldwide.
About the Author
Bradley Jones, Senior Vice President of Customer Experience
Brad Jones takes pride in his role as Senior Vice President of Customer Experience at Indeavor. With a wealth of experience in the manufacturing industry, Brad brings an arsenal of wisdom to Customer Operations, Business and IT teams to optimize the customer experience with best-in-class service delivery. Brad infuses his Supply Chain Operations knowledge into key components of the labor optimization strategy at Indeavor, bringing a fresh perspective for continued product and service enhancements. When Brad isn’t showing clients how to re-define their Operating experience, he enjoys spending every moment he can outside with his wife and 2 sons. To learn more or get in touch, connect with Brad on LinkedIn.